MascoLab
Filter Validation and Ancillary tests
Main regulatory and technical references: Annex 1, PDA TR No. 26, FDA Guideline Aseptic Processing, ASTM F838-15, USP <1663>, USP <1665
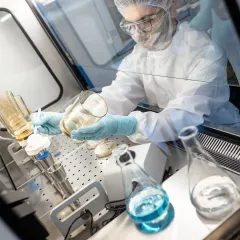
A viability test is performed by direct inoculation of the test microorganisms into the product for the process time; it allows the definition of test design of bacterial challenge
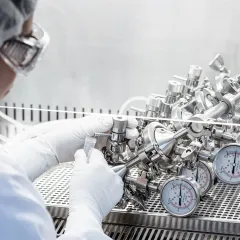
To demonstrate that the filtration process generates a sterile effluent and consistently removes a high level of standard bacterium (Brevundimonas diminuta, ATCC 19146) or process isolate, suspended in the product or surrogate fluid.
Test is performed in laboratory-scale optimizing the process fluid volume required and applying simulated worst-case process conditions.

To demonstrate that the filtration process and product does not alter the filter physical structure. The process filter is exposed to the product for the process time applying simulated worst-case process conditions.
The compatibility between product and filter is evaluated in terms of integrity test (for sterilizing-grade filter), visual inspection and main physical dimensions.
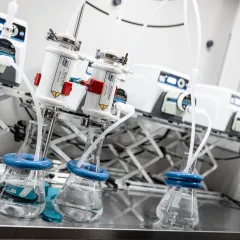
To demonstrate that the filtration process does not alter, under simulated worst-case process conditions, the quality of the drug product. Both non-specific (NVR and FTIR) and specific (GC/MS, Q-TOF and ICP/MS) analytical techniques can be performed to evaluate the presence of extractables compounds potentially toxic for patients.
Semi-quantitative analysis are applied to detect and quantify a wide range of extractables compounds. Following extractables results, specific toxicological assessment can be issued and, if needed, leachables test can be performed.

To demonstrate process filter integrity through test parameters (bubble point and/or forward flow) according to indication by filter suppliers.
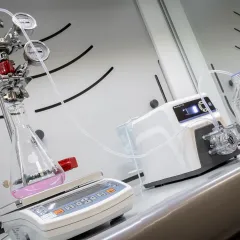
To evaluate the right sizing of the process filter and/or prefilter that allows the filtration of the process batch size according to the current filtration pathway and process parameters.
Different filters can be tested simultaneously to define the more suitable for process use. Test is performed in laboratory-scale optimizing the process fluid volume required.
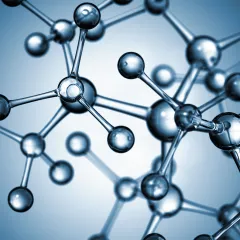
to demonstrate that the filter does not bind drug components affecting product specifications, e.g. API title decrease. Test is performed in laboratory-scale using small volumes of process fluid and applying simulated specific process conditions.
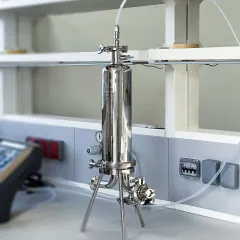
to determine and provide process filter integrity test parameters (bubble point and/or forward flow) wetted with specific product.